Acrylic is a translucent thermoplastic polymer known as “plexiglass” by the industry name.
It’s a polycarbonate-like material that can be utilised as an impact-resistant alternative to glass (specifically when PC has a high impact strength). It was first created in 1928, and it debuted on the market five years later.
Acrylic is one of the most transparent polymers available. Acrylic was utilised in periscopes and aeroplane windows, turrets, and canopies during World War II. Airmen who were injured by acrylic shards had a considerably better chance of survival than those who were wounded by glass shards.
Acrylic is now used in a wide range of settings, many of which take advantage of its natural transparency and resistance to damage caused by various types. Acrylic nails, paint, security barriers, medical devices, LCD displays, and furniture are only a few examples of the many ways it may be utilised. Due to its transparency, it’s frequently used for windows, tanks, and enclosures surrounding exhibits.
Why is acrylic utilised so often?
Acrylic is ideally suited for use in applications where transparency and resistance to high impact are required. Acrylic is considerably more scratch-resistant than transparent plastics. It’s a less heavy and more durable option than glass, as well as a cost-effective alternative to polycarbonate when strength isn’t critical.
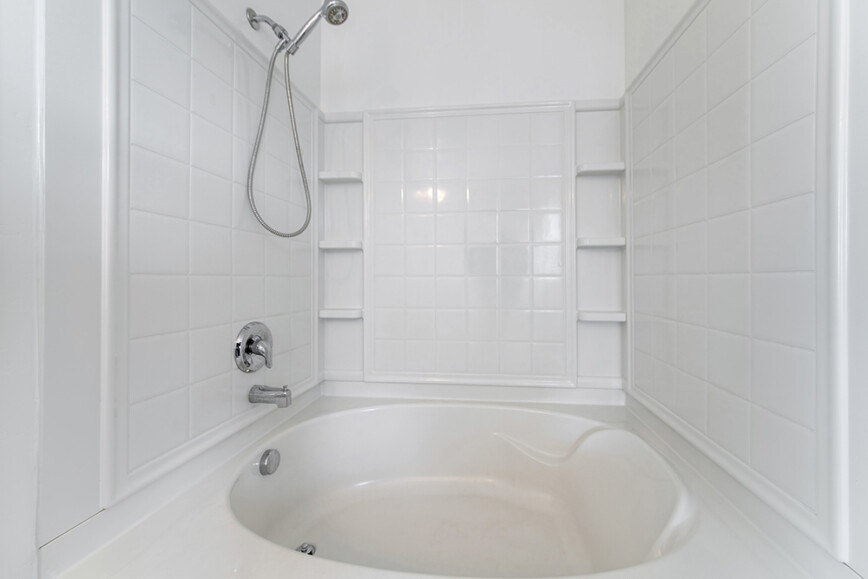
When laser light is focused on it, the material vaporises, making it possible to cut into extremely tiny forms using laser cutting techniques. Acrylic is a popular 3D printing material since it has a brittle failure and little strength. Instead, we generally utilise PC or PETG.
Despite the fact that PC and PETG aren’t as transparent as Acrylic, they are usually “clear enough” in most applications. If flawless clarity is essential, Acrylic is your only choice. We’ve also CNC machined and hand-shaped acrylic. After machining, several components require polishing to remove tool impressions and restore optical clarity, such as the following a lens, a replacement for glass or to display products.
What Are The Different Types of Acrylic?
Acrylic plastic, which is used in many aquariums, was first produced when formaldehyde was added to a solution of polyethene in 1843. In 1933, German chemist Otto Rohm sought a trading name for his product “plexiglass,” which he had invented. It’s produced by a variety of enterprises each with its own production process and proprietary combination. Trade names include recognised variants like Perspex, ELF Atochem’s Plexiglas®, or Lucite® by DuPont.
How is Acrylic made?
Acrylic plastic polymers are made by combining a monomer, such as a methyl methacrylate, with a catalyst. An organic peroxide is often used as a catalyst. The catalyst initiates the reaction and participates in it to keep it going, but does not become part of the final polymer.
Acrylic plastic sheets are made by bulk polymerisation. The monomer and catalyst are combined in a mould, after which the concoction is poured into the mould. Batch or continuous operation may be used to perform bulk polymerization: batch cell or continuous process.
Batch cells are the most common type, with capabilities ranging from 0.06 to 6 inches (0.16-15 cm) in thickness and width, producing acrylic sheets of a variety of sizes. This method may also be used to create rods and tubes. The continuous method is more efficient and quicker. It’s used to make smaller sheets of a lesser width and thickness than those produced using the batch cell technique.